- Home
- Eletronics & Semiconductor
- Foundry Market
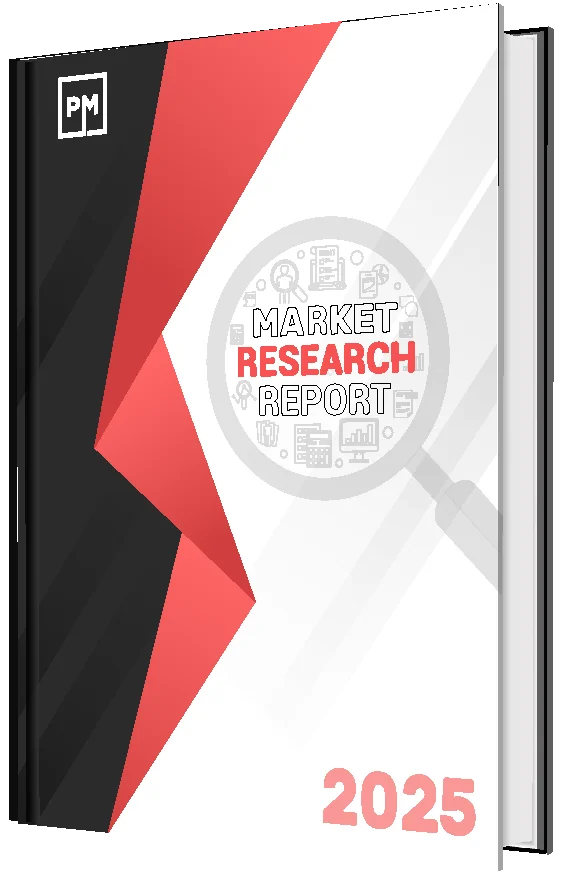
Foundry Market Size, Share, Growth, and Industry Analysis, By Type (Ferrous Foundry, Non-ferrous Foundry, Die Casting, Sand Casting and Investment Casting), By Application (Automotive, Aerospace, Construction, Heavy Machinery and Industrial Equipment), and Regional Forecast to 2033
Region: Global | Format: PDF | Report ID: PMI2835 | SKU ID: 29768585 | Pages: 105 | Published : July, 2025 | Base Year: 2024 | Historical Data: 2020 - 2023
FOUNDRY MARKET OVERVIEW
The global Foundry Market size is forecasted to reach USD 162.33 billion in 2025, growing further to USD 273.79 billion by 2033 at an estimated CAGR of 5.98% during the forecast period.
The world's foundry market is an essential cog in the manufacturing wheel, with ferrous metal castings being an essential component across a multitude of demand businesses including auto and aerospace, construction and ag equipment, power generation, and marine. Foundries make parts ranging from engine blocks, cylinder heads, pump housings and valves to rocker arms, brackets and structural supports by melting metal and pouring it into molds to create the required shape. The most popular materials are gray iron, nodular iron, aluminium, steel, bronze and magnesium actuators are now quite common, and growing need for light parts will lead to use of high strength alloys as well as non-ferrous materials.
While industries move ahead towards excellence and performance improvement, the foundry market is having a sweeping tendency towards high-precision casting, CAD, casting, solidification software programs and 3D printing for patterns, moulds and cores. These innovations lead to increased casting accuracy, fewer mistakes and faster lead times. The foundries are also deploying automation and robotics technology in molding, pouring and finishing to improve repeatability and lower labour costs. Moreover, industry trends towards sustainability and emission control are driving the adoption of energy-saving furnaces, closed-loop sand reclamation systems, and improved waste management programmes. Asia-Pacific, in particular by China and India, dominates foundry production number as a result of the presence of large production and cheaper labour cost as well as the increased demand in automotive. At the same time, North American and European foundries are modernizing operations, embracing Industry 4.0 technologies and environmentally friendly practices to stay viable. While challenges, such as high-power consumption, fluctuating raw material costs, and shortage of skilled labour persist, the foundry industry is ready for expansion powered by digital transformation, infrastructure efforts, and the worldwide move towards decentralizing manufacturing.
KEY FINDINGS
- Market Size and Growth: The global Foundry Market is projected to grow from USD 162.33 billion in 2025 to USD 273.79 billion by 2033, with a CAGR of 5.98%.
- Key Market Trends: Integration of Industry 4.0, including automation, robotics, and digital twins, is transforming production efficiency and quality.
- Key Market Drivers: Strong demand from automotive and aerospace, which together account for nearly 60% of total foundry castings.
- Technological Advancements: Adoption of smart foundry solutions, IoT-enabled defect detection, and AI-driven casting simulation is gaining traction globally.
- Regional Growth: Asia-Pacific holds the largest market share, producing about 70% of global foundry castings due to China and India’s scale and cost advantages.
- Type Segmentation: Ferrous Foundry remains dominant, representing over 50% of the market by volume for structural and automotive parts.
- Application Segmentation: Automotive is the largest application, holding about 45% share driven by lightweight and high-strength casting needs.
- Key Players: S&P Global Market Intelligence (U.S.) is noted for its industry analytics leadership, commanding about 25% share in foundry data solutions.
RUSSIA-UKRAINE WAR IMPACT
"Foundry Market Had a Negative Effect as raw material supply chains, energy prices, and regional demand during the Russia-Ukraine War"
The Russia-Ukraine war has had a profound impact on world foundry So far, The Russia-Ukraine war had exerted much influence on the world foundry by affecting the supply chain of raw materials and energy prices, as well as the regional demand. Critical metals such as pig iron, steel billets and ferroalloys, used in foundry operations around the globe, are provided by Russia and Ukraine. The war has produced export restrictions, port closures and logistical backlogs and has caused price volatility and shortages of materials, especially in Europe, which had become particularly dependent on imports from the region. This disruption has prompted manufacturers to look for other sources or curtail output, which has put pressure on margins and delivery dates.
The war has also sent energy prices spiralling to record highs, most notably for natural gas and electricity, needed for smelting and casting of metal. In Europe, foundries, which were already strained by tough environmental rules, have seen a spike in operational costs, causing some to temporarily close and others to turn more to energy-efficient equipment. The ever-changing landscape has also led to hesitant investment in some Eastern European foundry projects, as well as prompted the attraction of reshoring and supply chain diversification, particularly in Asia-Pacific and North America. More broadly, the Russia-Ukraine war has laid bare cracks in the global foundry supply chain, and has raised the urgency of more regional sourcing, digitized planning, and energy efficiency.
LATEST TREND
"Integration of Industry 4.0 in Foundries to Drive Market Growth"
The increasing penetration of Industry 4.0 solutions such as automation, robotics, AI and IoT is one of the key trends that's reshaping the foundry market. A number of smart systems have been developed to maximise production processes, monitor in real-time, and improve quality control in foundries. By using automated pouring, molding robots and sensors for identifying defects, there’s less chance of human error, shorter processing times and equipment can be used in a more predictive manner. The progress is enabling foundries to minimize waste, enhance yields and deliver consistent product quality, each of which is key for serving the burgeoning demand in verticals that include automotive and aerospace. Additionally, process optimization based on data allows for an increased efficiency and the ability to react to changing customer needs. At the same time, penning of digital twin technology and casting simulation software is skyrocketing. They enable engineers to simulate the casting process to examine options for material flow, solidification and cooling before production starts. This reduces expensive errors, shortens the time required to design a product and commemorates customized development. With rising global competition and increasing customer requirements for more challenging, lightweight and sustainable components, digitalization is coming out of the competitive advantage box and into the realm of basic requirements for a foundry’s survival and growth in today’s modern industrial environment.
FOUNDRY MARKET SEGMENTATION
BY TYPE
Based on type, the global market can be categorized into ferrous foundry, non-ferrous foundry, die casting, sand casting and investment casting
- Ferrous Foundry: Ferrous foundries produce cast iron and cast steel parts, products, and components, which are commonly used in construction, automotive, and heavy equipment industries, among others, for its strong and durable characteristics. Such foundries are the leading producers in the market by volume, especially for engine blocks, pipes, pumps and other structural components.
- Non-Ferrous Foundry: Some of the most-highlighted metals that non-ferrous foundries work with are aluminum, copper, zinc and magnesium which are used to create lightweight parts. This market is rising on account of growing applications in automotive and aerospace industry owing to Transportation fuel efficiency and low weight initiatives.
- Die Casting: Die casting features high-pressure injection of molten metal into steel cavities, and is suitable for high-volume production of accurate parts. It has had great success in automotive and consumer products as it provides a high quality, smooth surface finish, good dimensional accuracy level and repeatability.
- Sand Casting: Sand casting is a versatile, economical process for small lot production and especially for large parts. It's commonly used to make housings, cylinder heads and other challenging geometries in heavy equipment for industrial markets.
- Investment Casting: Investment casting is typically more accurate and has better surface finish than sand-casting, and is used for more complex shapes usually used for aerospace components, medical parts and defence components. While more expensive, it is perfect for parts that need tight tolerances and complicated design.
BY APPLICATIONBased on application, the global market can be categorized into automotive, aerospace, construction, heavy machinery and industrial equipment
- Automotive: In the automotive industry, castings are used in the production of engines, transmission, brakes and suspensions. Foundries supply that part of the market with aluminum alloys and high-strength ferrous parts that comply with performance and fuel-efficiency requirements.
- Aerospace: Precision and lightweight strength are key to aerospace applications, creating a market for non-ferrous and investment castings. Turbine blades, airframe components, and landing gear components are being manufactured more and more by advanced foundry methods.
- Construction: Applications for building and construction include castings for frames, fittings, reinforcement, and tools. This industry requires heavy duty large parts, many of them made using ferrous sand casting.
- Heavy Machinery: Foundries produce heavy-duty components for ag, mining, and industrial machines, such as gears, housings and load-bearing components. These parts need to be sturdy in tough service, and so are favor sand and ferrous casting.
- Industrial Equipment: In this category, machineries and general equipment which are used for manufacturing, HVAC, as well as pumps and compressors are included. This is the all-around itinerant segment which includes ferrous and non-ferrous foundries looking for both cost-effective solutions and high quality.
MARKET DYNAMICS
Market dynamics include driving and restraining factors, opportunities and challenges stating the market conditions.
DRIVING FACTORS"Growth in Automotive and Aerospace Manufacturing to Boost the Market"
The rising demand from automobiles and aerospace industry, two major consumers of the cast components for critical applications, is driving the foundry market growth. In the automobile industry, weight reduction of vehicles in response to fuel efficiency standards and the control of carbon dioxide is promoted and a demand for aluminium and magnesium castings has been increased. Foundries are adjusting to this by casting lighter engine blocks, transmission casings and EV elements through nonferrous and die casting techniques. Also, the sharp rise of electric vehicles (EVs) is driving new demand for tailored cast parts such as battery cases and motor casings. In aerial industry, the demand for high complex and resistance-to-temperature parts the market of investment and advanced sand casting for engine components, turbine blades and landing gear structures is likely to grow. Growing global air fleet, soaring air travel and defense fleet modernization are a few of the factors that are driving the demand for aerospace casting. These industries require tight tolerances, light weight, and high strength, and these are challenges that contemporary foundries can meet. Combined, automotive and aerospace production constitute two of the primary drivers of foundry market expansion.
"Technological Advancements and Industry 4.0 Integration to Expand the Market"
The integration of automation, robotics and the digital factory represents the most competitive production process for the foundry of the future and is creating new structured economic growth. Foundries are also adopting the use of robots for pouring and automated handling and inspection systems which decrease reliance on manual labour, decrease the risk of defects and allows for faster throughput. These advancements. are driven by the need to accommodate the increasing demand for high volume and complex parts in areas ranging from industrial equipment, transportation and construction. Moreover, simulation software has made digital twins available to the foundry, enabling the foundry to test and develop its designs virtually, well before production gets underway, greatly reducing the costs of scrap and lead times. When IoT (Internet of Things) sensors are combined with AI-based data analytics, factory operators are able to track furnace temperatures, the flow of metal and defect patterns in real time, contributing to improved predictive maintenance and operational efficiency. This move to smart foundries drives both cost-competitiveness and customisation, and increases flexibility, so that foundries can adapt more quickly to changing market-requirements. Growing popularity of smart manufacturing is a key driver of the global foundry market.
RESTRAINING FACTOR
"High Energy Consumption and Environmental Regulations to Potentially Impede Market Growth"High energy consumption in the melting, molding, and finishing of metal, and the tightening of environment regulations are one of the key growth inhibitors in the global foundry industry. Foundries are energy-hungry operations, burning fossil fuels and using electric furnaces to melt metals at extreme temperatures. This results in tremendous carbon emission, waste of heat and air pollution, which are of great concern to the government regulators around the world. Regulatory authorities in North America, Europe and certain regions of Asia are formulating stringent emission standards, energy efficiency norms and waste disposal practices, for production facilities. Now a days foundries need to invest in expensive pollution control equipment, pollution monitoring, energy saving devices etc., for maintaining the compliance. Small and second echelon foundries find it difficult to support such capital costs and can become less competitive or close down entirely. Moreover, intricate disposal of foundry sand, slag and hazardous waste is to be done carefully and by specialized treatment, resulting in incurring of higher operating costs. These environmental and energy-strong limitations not only increase production costs but also act as a scale-inhibiting factor of foundries in many areas without equally affordable and clean energy alternatives, which is a constraint of the total market growth.
OPPORTUNITY
"Rising Demand for Lightweight and Customized Components To Create Opportunity for the Product in the Market"
There is a substantial opportunity in the world market of foundry due to growing demand for light weight and tailor-made metal components particularly in automotive, aerospace and medical industry. As manufacturers struggle in response to declining market opportunities to reduce fuel consumption, carbon emissions and weight of product, the requirement for advanced casting solutions incorporating lightweight metals, including aluminium, magnesium and titanium, is growing. Those foundries, able to support this trend by supplying, lightweight and strength structurally low casting tolerance precision casting will have a permanent competitive advantage. Further, an increasing proliferation of electric vehicles (EVs), drones and compact industrial equipment is driving the need for complex, customised parts in smaller volumes. This move dovetails with foundry investments in 3D printing for mold making, computer-aided casting design, and digital simulation tools to facilitate mass customization without sacrificing quality or lead time. Medical and orthopaedic brackets and aerospace brackets are some high margin applications of which you can profit by creating custom casting solutions. Further, foundries that introduce smart manufacturing and flexible production systems will also be in the position to attract new business as OEMs and tier-1 suppliers strive for more localized and nimble manufacturing partners. This evolution represents a significant growth opportunity for forward-thinking, technology-driven, and environmentally minded foundries around the globe.
CHALLENGE
"Skilled Labor Shortage and Workforce Modernization Could Be a Potential Challenge for Consumers"
A critical challenge facing the global foundry market is the shortage of skilled labor and the increasing difficulty in attracting and retaining a modern workforce. Foundry operations involve complex tasks such as mold preparation, metal melting, pouring, finishing, and quality inspection—many of which require hands-on expertise, safety awareness, and physical endurance. However, the sector has long struggled with an aging workforce and a limited influx of young, technically trained professionals. The perception of foundry jobs as dirty, physically demanding, and less technologically advanced than other manufacturing sectors has led to a declining interest among newer generations. As a result, foundries worldwide are encountering difficulties in filling critical roles, especially in pattern making, metallurgical analysis, maintenance, and robotics operation. At the same time, the ongoing shift toward automation and digital technologies demands a new skill set—workers proficient in operating CNC machines, simulation software, and data analytics tools. This skills gap between traditional foundry processes and emerging digital practices hinders the industry’s ability to scale efficiently and adopt smart manufacturing. Without strategic workforce development, training programs, and better industry branding, the labor shortage will continue to be a bottleneck in the long-term growth of the foundry market.
FOUNDRY MARKET REGIONAL INSIGHTS
-
NORTH AMERICA
The United States foundry market remains one of the most technically advanced in the world, supported by a diverse industrial base including automotive, defense, aerospace, and heavy machinery sectors. Although the total number of foundries has declined over the decades, the remaining facilities are increasingly high-tech, with strong adoption of Industry 4.0 practices, including simulation software, robotic automation, and predictive maintenance systems. Rising demand for electric vehicles and sustainable infrastructure has encouraged American foundries to invest in non-ferrous and precision casting capabilities. Additionally, the trend of reshoring and localizing supply chains post-COVID-19 and amid geopolitical tensions is driving U.S. manufacturers to partner more with domestic foundries. However, labor shortages and strict environmental regulations continue to challenge operational scalability.
-
EUROPE
Europe accounts for a significant foundry market share, particularly in countries like Germany, France, and Italy, where precision engineering and high-performance automotive components dominate demand. European foundries are globally recognized for their craftsmanship and innovation, particularly in investment casting and sand casting for aerospace and industrial applications. However, the region faces strong regulatory pressure to reduce emissions and energy consumption. This has accelerated the shift toward energy-efficient melting systems, closed-loop sand reclamation, and decarbonization initiatives. European foundries are also focusing on digital integration to maintain competitiveness, with emphasis on quality, sustainability, and customization for export-oriented markets.
-
ASIA
Asia-Pacific leads the foundry market in terms of volume and cost-effective production. China, the world’s largest producer of castings, continues to dominate due to mass manufacturing, export strength, and domestic consumption across automotive, electronics, and infrastructure sectors. India is also emerging as a global hub for castings, especially for ferrous and non-ferrous components in automotive and industrial machinery. The rapid pace of urbanization and industrialization, combined with government incentives like “Make in India,” is attracting global OEMs to partner with local foundries. Though traditionally focused on high-volume, low-cost output, foundries in this region are increasingly investing in automation, casting simulation, and quality improvement to move up the value chain and expand their global footprint.
KEY INDUSTRY PLAYERS
"Key Industry Players Shaping the Market Through Innovation and Market Expansion"
Leading players in the global foundry market are focusing on technological innovation, capacity expansion, and sustainability to strengthen their market position and meet evolving industry demands. Major foundries are increasingly adopting automation, robotics, and digital monitoring systems to enhance casting precision and reduce defects, particularly in high-demand sectors such as automotive, aerospace, and industrial equipment. Many companies are investing in energy-efficient melting furnaces and closed-loop sand reclamation systems to comply with environmental regulations and reduce operational costs. Additionally, global foundry operators are expanding their non-ferrous and precision casting capabilities to cater to the rising demand for lightweight components, especially for electric vehicles and aircraft. Some players are also forming strategic partnerships with OEMs and investing in smart manufacturing to offer customized, value-added casting solutions. These efforts are enabling foundry companies to not only improve efficiency and output quality but also future-proof their operations amid supply chain disruptions and labor shortages.
LIST OF TOP FOUNDRY MARKET COMPANIES
- IDG (U.S.)
- S&P Global Market Intelligence (U.S.)
- IHS Markit (U.S.)
- Gartner (U.S.)
- Forrester (U.S.)
KEY INDUSTRY DEVELOPMENT
January 2024: S&P Global Market Intelligence (United States) launched an enhanced AI-powered analytics platform designed specifically for industrial manufacturing and supply chain analysis. This new solution integrates real-time foundry production metrics with commodity price forecasting, enabling foundry operators and investors to make data-driven decisions more effectively. The upgrade also included ESG (Environmental, Social, and Governance) performance tracking, addressing the growing demand for sustainability in the foundry market. This development reflects the shift toward digital intelligence tools in industrial planning and underscores S&P’s strategic focus on supporting heavy industries with smart, actionable insights.
REPORT COVERAGE
This report provides a comprehensive analysis of the global foundry market, offering detailed insights into current market dynamics, growth drivers, restraints, challenges, and emerging opportunities. It examines industry trends, technological developments, and regulatory landscapes that influence the foundry value chain. The report also assesses the impact of key geopolitical events and macroeconomic shifts on raw material availability, energy consumption, and regional demand patterns. In-depth market estimates and forecasts are provided in terms of value (USD billion) and volume (tons), covering historical data and projections across multiple timeframes.
The study includes market segmentation by product type (Ferrous Foundry, Non-ferrous Foundry, Die Casting, Sand Casting, Investment Casting) and application (Automotive, Aerospace, Construction, Heavy Machinery, Industrial Equipment). Regional insights span North America, Europe, Asia-Pacific, and Rest of the World, highlighting key trends, competitive landscape, and strategic initiatives in each region. The report also profiles leading industry players, their technological advancements, capacity expansions, partnerships, and sustainability efforts. Key industrial developments and innovations are analyzed to help stakeholders understand market positioning and long-term potential.
Attributes | Details |
---|---|
Historical Year |
2020 - 2023 |
Base Year |
2024 |
Forecast Period |
2025 - 2033 |
Forecast Units |
Revenue in USD Million/Billion |
Report Coverage |
Reports Overview, Covid-19 Impact, Key Findings, Trend, Drivers, Challenges, Competitive Landscape, Industry Developments |
Segments Covered |
Types, Applications, Geographical Regions |
Top Companies |
IDG, Gartner, Forrester |
Top Performing Region |
North America |
Regional Scope |
|
Frequently Asked Questions
-
What value is the foundry market expected to touch by 2033?
The global foundry market is expected to reach 273.79 billion by 2033.
-
What CAGR is the foundry market expected to exhibit by 2033?
The foundry market is expected to exhibit a CAGR of 5.98% by 2033.
-
What are the driving factors of the foundry market?
Growth in automotive and aerospace manufacturing and technological advancements and industry 4.0 integration to expand the market growth.
-
What are the key foundry market segments?
The key market segmentation, which includes, based on type, the foundry market is ferrous foundry, non-ferrous foundry, die casting, sand casting and investment casting. Based on application, the foundry market is classified as automotive, aerospace, construction, heavy machinery and industrial equipment.
Foundry Market
Request A FREE Sample PDF